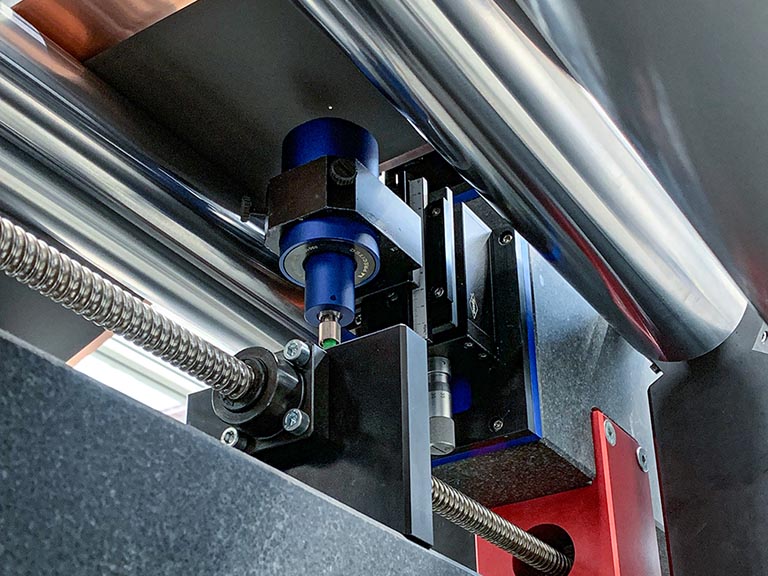
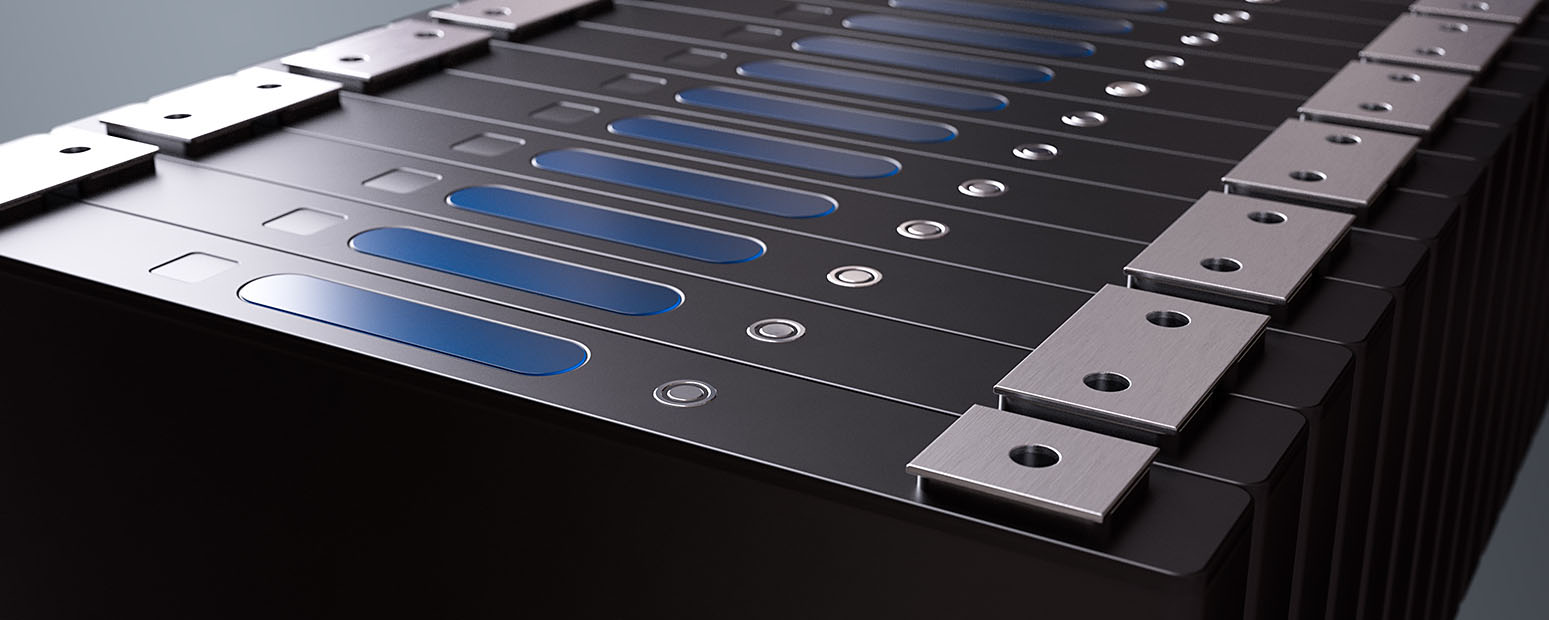
生产锂离子电池的高效解决方案
在电极生产过程中,正负极片交替层叠而成,并由俗称的隔膜隔开。之后,卷起金属极片,将其装入金属外壳,最后将电池焊接牢固。
我们的质量控制系统用于多个工艺步骤,以确保电池的高效生产。例如,极片厚度测量、切割毛刺测量、以及极片层的激光焊接(极片到极耳)或外壳和正极的激光焊接(盖到罐)。
客户的明确要求是:精确度 < 1 μm。我们的传感器符合这一要求,并针对电池生产环境进行了优化,即所谓的卷对卷应用:
- 高卷速
- 振动电极片
- 光滑和黑色表面
在激光技术中,盖到罐的激光焊接是一项重要应用。在这种情况下,必须检测到针孔,或者最好是完全避免针孔。我们专门针对这些应用优化了我们的产品和光学元件,并开发了创新的解决方案。
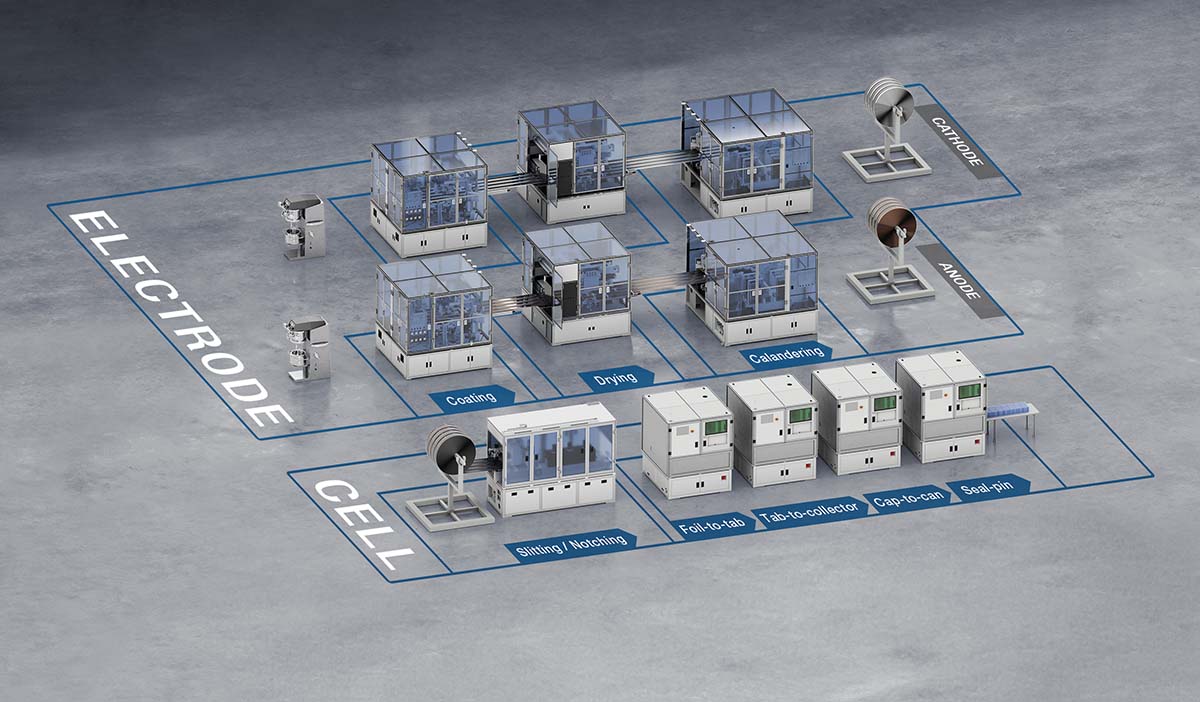
电极生产步骤的解决方案
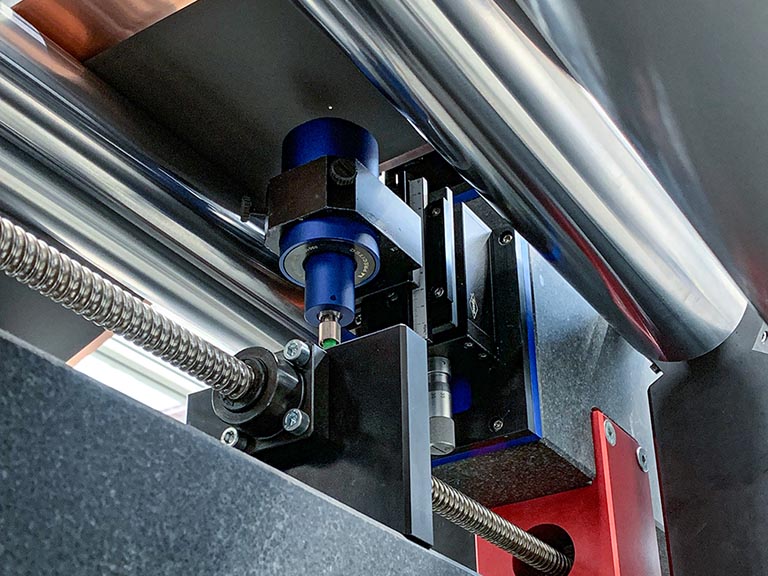
电极极片的精准涂布厚度对电池的性能和使用寿命有重要影响,因此起着至关重要的作用。在生产过程中,首先在载体薄膜上连续或间歇地涂覆浆料,然后在干燥通道中去除涂布上的溶剂。
在干燥过程前后都要进行厚度测量。涂布可以是干的,也可以是湿的,也就是说,无论表面是反光的、黑色的还是多孔的,我们的测量都是精确的。振动和皮带速度的影响会得到补偿。对薄膜的波纹和厚度进行精确分析,并显示结果。目前的市场要求是绝对精度 < 1 µm,重复精度 ± 0.5 µm。
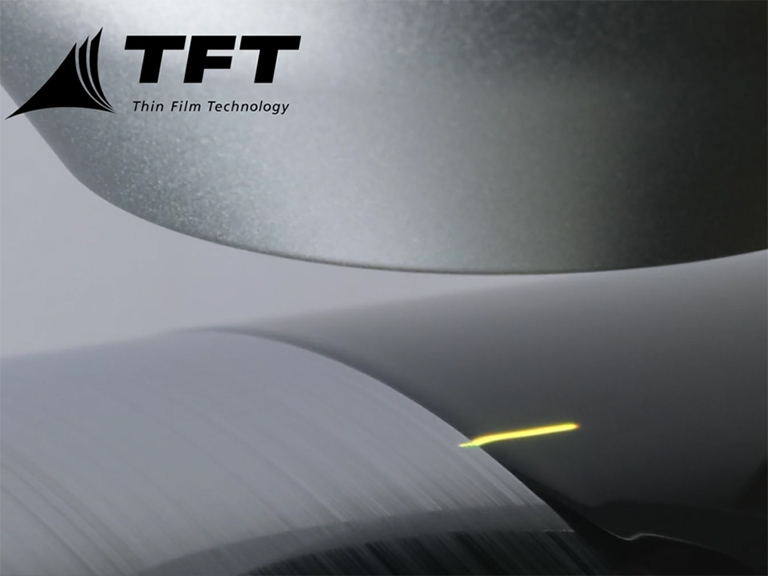
边缘超高发生在涂浆的边界,会对电极的进一步加工产生负面影响,尤其是在卷绕过程中。它可能导致不对称卷绕,从而产生大量的处理问题。
为了提高电池的性能,目前正在尝试增加涂布的厚度。然而,较厚的涂布也容易形成边缘超高。
我们的线传感器能够在生产过程中精确测量长达 20 毫米的边缘。湿边和干边都能检测到。在此过程中会计算极片的振动。可精确显示从反光金属载体极片到黑色浆料的过渡。
起始/停止边缘出现在间歇涂布过程中。在此过程中,浆料会交替涂抹到载体极片上或故意不涂抹。对于这种类型的涂层,起始/停止边缘具有挑战性,必须对其进行监控,以确保电池的使用寿命和安全性。
使用我们的点传感器可以精确测量地形轮廓,从而及早准确地检测出可能存在的涂布缺陷。
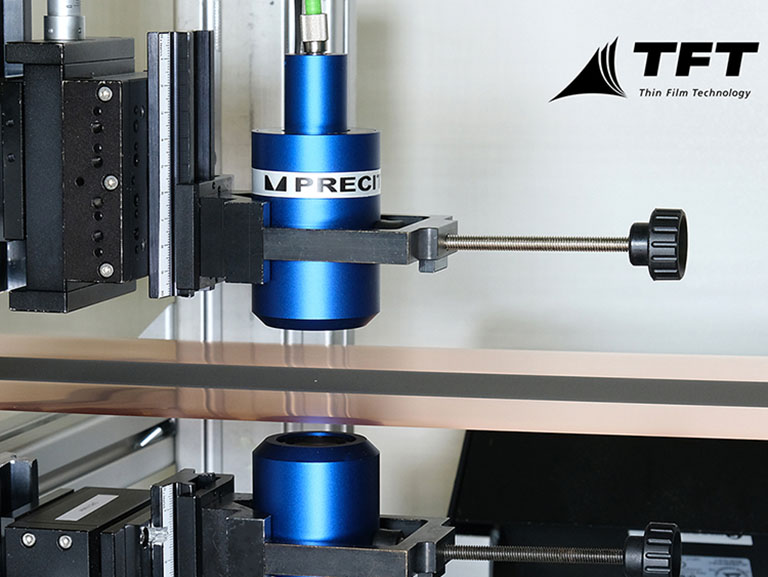
电极极片的确切涂层厚度对电池的性能和使用寿命有重要影响,因此起着至关重要的作用。在生产过程中,首先在载体极片上连续涂上浆料,然后在干燥通道中加热去除溶剂。为了保证浆料在载体薄膜上的高粘合强度,对 5 个干燥阶段的识别至关重要。例如,必须防止粘合剂的迁移。为了优化干燥,孔隙完全排空的时间也至关重要。
我们的传感器可以在干燥过程中识别这些时间点。这样可以缩短干燥时间,优化涂层质量,降低能源成本。
在整个干燥过程中,还可以进行精确的厚度测量。无论是湿层还是干层、黑色还是多孔石墨或阴极活性材料,测量结果都能保持精确。在测量过程中,振动和传送带速度的影响都会得到补偿。使用传感器可以缩短干燥时间,优化涂层质量,节省能源成本。
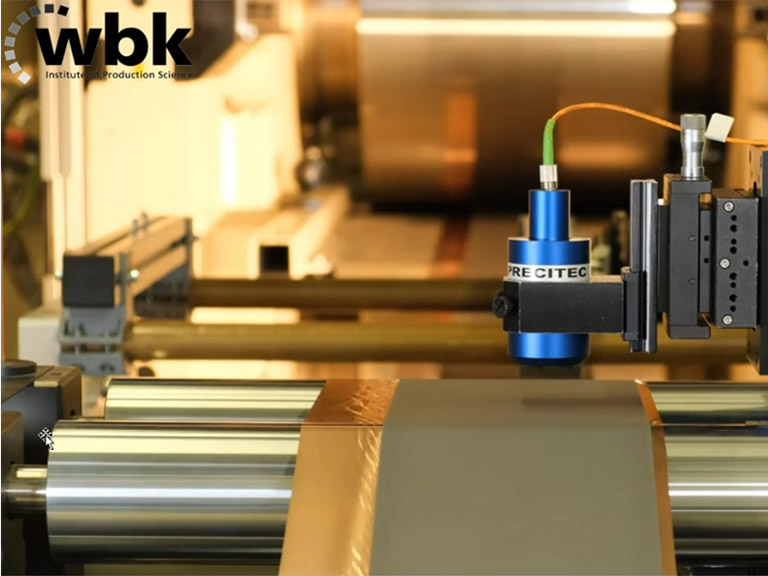
辊压是电极生产的最后一道工序。涂布的最终厚度和孔隙率主要取决于这一步。除了单位面积重量外,这些也是电池性能和安全性的决定性特征。
我们的传感器可对辊压过程进行全面测量。可以测量辊压前后的电极厚度、辊压辊的同心度以及俗称的褶皱。这些都是基材上涂布边缘的褶皱。我们的传感器会对铝极片的振动进行补偿,并计算出波浪度。这意味着,即使在 100 - 150 米/分钟的高速传送带上,也可以随时进行精确测量。
压延辊是直径大于 1 米的实心钢辊。镜面表面经过精确研磨,以确保轧制出最高质量的电极。轧制表面的缺陷以及同心度的微小偏差都会直接影响电极极片的厚度和状态。因此,监测压延辊表面的磨损和同心度至关重要。
我们的传感器可以记录这些质量特性。同心度的最小偏差和压延辊表面的最小划痕都能被检测出来。
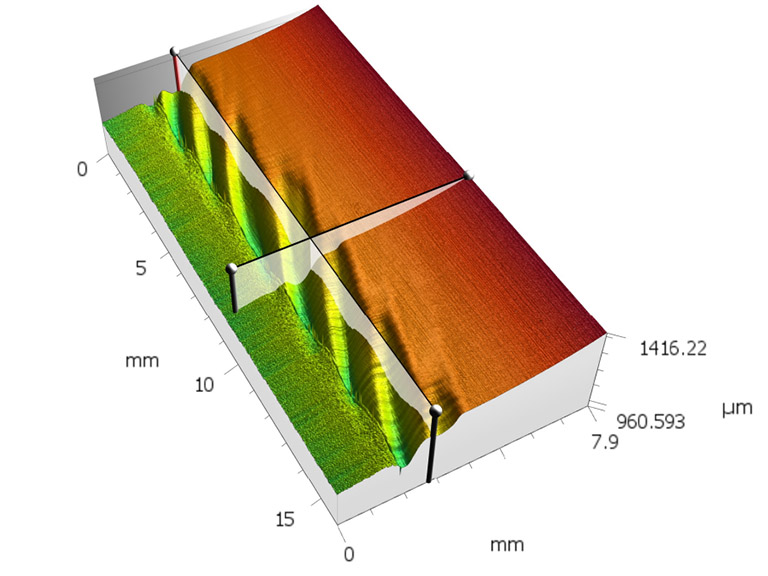
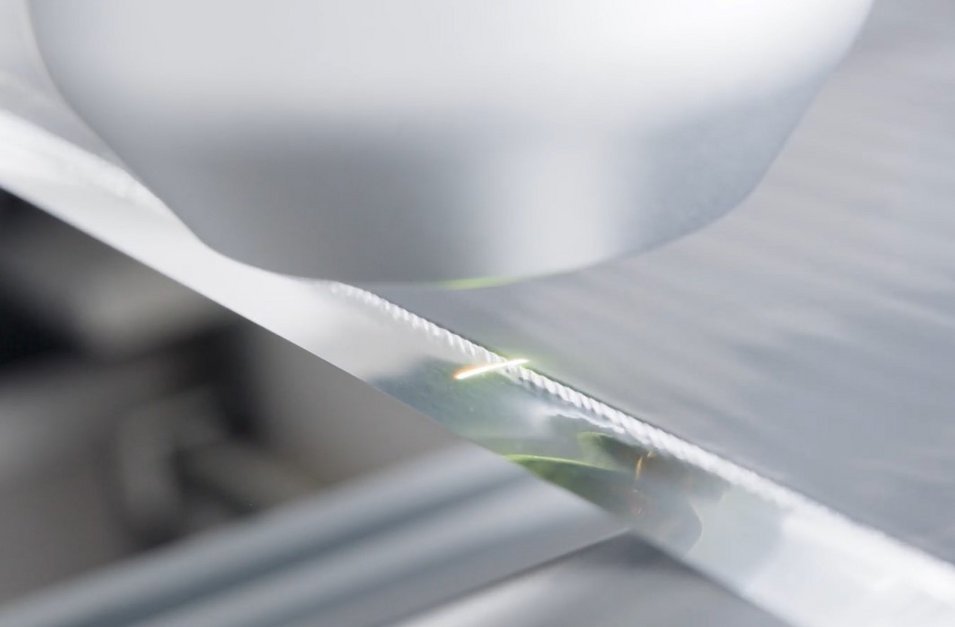
由于轧制力以及涂层和箔片材料的不同膨胀性,轧制后会产生褶皱。尤其是在导电箔与涂层的边缘。褶皱会大大增加后续生产工艺的复杂性,甚至使其无法进行。
利用我们的传感器技术,可以检测到褶皱并测量其大小。如果褶皱过大,材料就会被剔除。还可以通过调整轧制参数来减少褶皱的形成。
隔膜片将两个电极极片(即阳极和阴极)隔开,从而防止短路。隔膜片必须具有电绝缘性,因此通常由多孔塑料(有时是多层塑料,如聚丙烯或聚乙烯)组成。这些薄膜的厚度在 15 至 25 µm 之间,不得被外来颗粒损坏。如果隔膜片被穿透,就会造成短路,极有可能引发火灾(热失控)。
利用我们的传感器,我们可以测量隔膜片的厚度和完整性,并解析单个膜层的厚度。
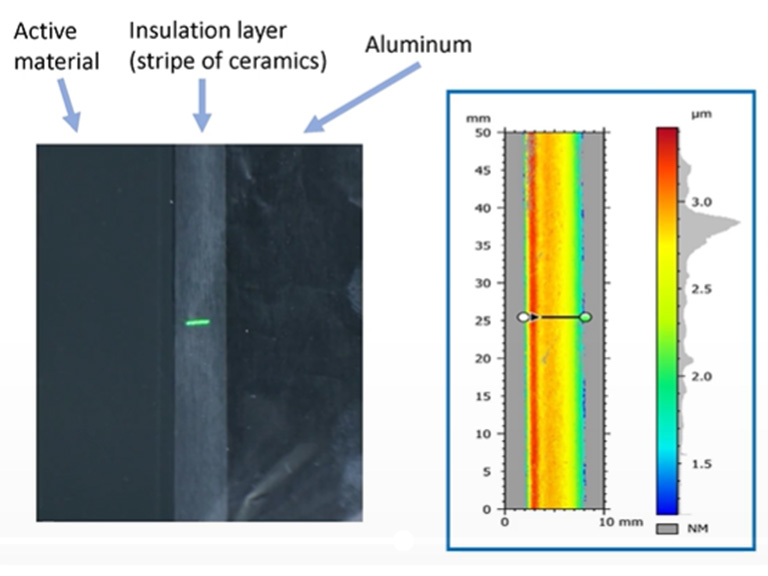
为了提高电池的安全性,有时会在电极上涂一层绝缘层。绝缘层由紧贴活性材料的陶瓷涂层组成。
原因是聚丙烯隔膜在 110°C 的温度下会收缩,甚至在 150°C及 以上的温度下会熔化。陶瓷涂层可以防止阴极和阳极之间发生短路的潜在风险,从而提高电池的安全性。
绝缘涂层的标准厚度为 3 µm - 10 µm。为了达到最佳质量和高效生产,这些厚度都是在卷对卷工艺中在线实时测量的,即使在带材速度高达 150 米/分钟的情况下也是如此。例如,可以显示氧化铝(Al2O3)的厚度剖面并检测缺陷。可以检测出活性材料和陶瓷涂层之间可能存在的间隙,还可以观察到陶瓷涂层与活性材料之间的重叠。
电池生产步骤的解决方案
为了实现电极箔的直线切割,Precitec 开发了所谓的“基于开槽滚筒的气体辅助激光切割”解决方案。这一创新技术通过在切割过程中精确导引箔材并最小化振动,确保了始终如一的高切割质量。通过在滚筒上直接进行切割,可显著减小激光光斑尺寸并降低平均激光功率,从而显著减少热影响区(HAZ),进一步优化整体切割质量。
气体辅助激光切割还提供了更清洁、更高效的加工过程。切割过程中产生的颗粒和残留物被引导进入开槽滚筒,并通过集成的抽吸系统安全地清除,从而有效防止激光切割系统受到污染。
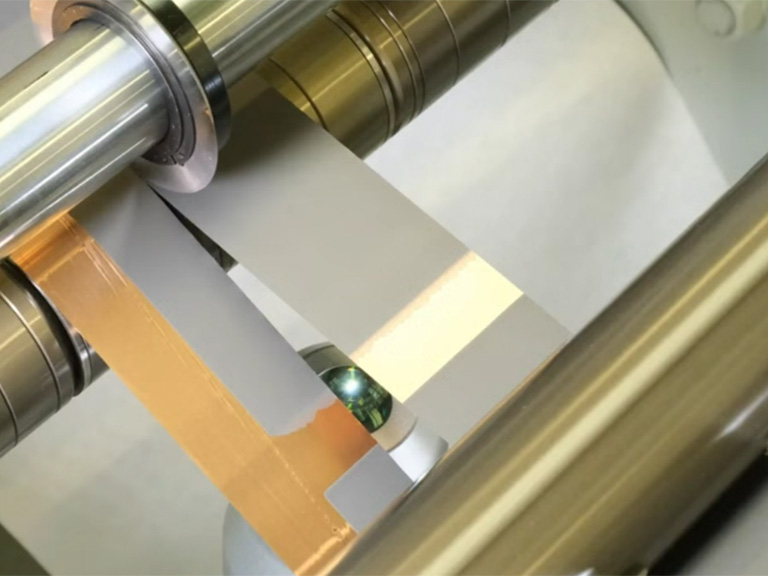
如果隔膜片被击穿,就会发生短路,并极有可能引发火灾(热失控)。隔膜的厚度通常约为 20 µm。因此,检测约 10 µm 的切割毛刺至关重要。
对毛刺的测量可以显示金属极片的几何形状和形状,以及涂布(包括底层金属极片)的形貌。根据不同的任务和要求,可采用不同的技术从下方或侧面测量毛刺。与卷对卷系统集成后,我们可以可靠地检测毛刺,从而提供有关分切机(预测性维护)或激光切割质量的信息。
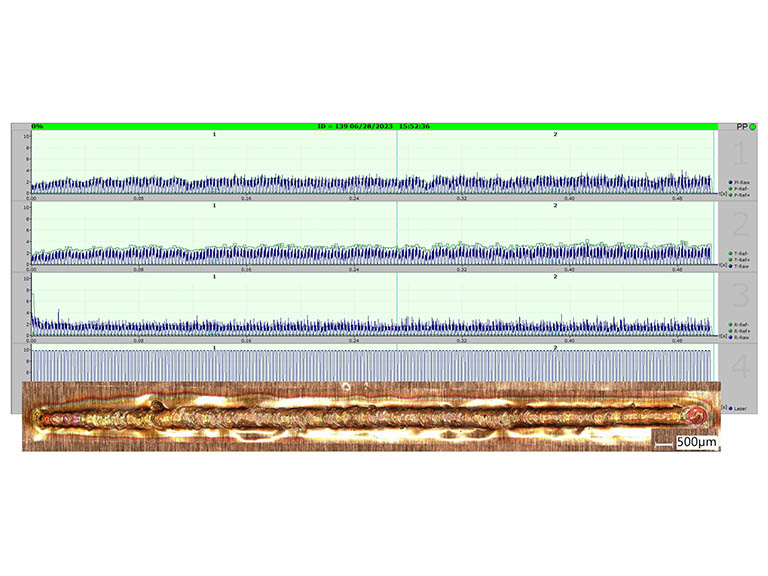
电池单元由多层薄铜箔和铝箔(5-10μm)组成,这些薄铜箔和铝箔必须焊接在一起,才能形成稳定强大的电池。在此过程中,通常要将60-100片铜箔焊接在一起。然后,根据电池所需要的容量和性能,将几层这样的薄片堆叠在一起。
在焊接叠片时,除了要精准夹紧叠片外,智能焊接策略也很重要。这样才能实现从第一层膜到最后一层膜之间的安全连接,且变形小、无烧穿现象。通过使用过程监控系统,可以检测到焊接异常和最小偏差,从而确保焊缝的可靠性。最终形成更高的产量和更好的质量。
查看更多信息
封口焊接是将金属盖(帽)焊接到金属容器(罐)上。这种激光焊接通常用于电池生产,达到将电解液与外界隔离,防止液体泄露的目的。这里使用的焊接材料是铝或者镀镍钢。
封口焊接不仅用于圆柱形电池芯,也用于棱柱形电池芯。在这两种生产过程中,焊接质量对电池的性能和可靠性都起着至关重要的作用。
对于4680这类的大型电池,电池罐的圆度并不总是100%。但是,激光束必须沿着电池罐的轮廓运作,这是焊接严密性的重要前提。使用ScanMaster可以快速准确地测量实际轮廓,并相应地调整激光束。这样就可以实现高质量的焊缝,而无需焊接到罐体上。
帽-罐激光焊接地一个典型缺陷就是所谓的针孔,它会导致焊点泄露。激光焊接监控器可将大的针孔作为焊接异常检测出来。焊缝上的最小缺陷可在后期处理过程中通过测量焊缝的形貌检测出来。这样就可以实现重新加工不过关的电池单元,减少废品产生。
在电池组组装过程中,电解质液要均匀、完全地注入电池组,以确保最佳的性能。电池外部的电解液残留会影响产品安全。电池生产量越大,在生产线上自动检测和剔除电池片填充侧的污染区域的需求就越迫切。在随后进行的被称为密封销焊接的工序中,圆柱形电池或棱柱形电池的填充口将通过激光进行密封焊接。电解液的残留物会影响焊缝的质量,并且可能导致泄露和焊接飞溅物严重污染。由此会导致电池的泄露,从而形成废品。
向电池单元注入电解液后,用盖子封闭注入口,通过激光进行紧密的焊接。密封的电池有效防止了电解液的溢出。
电池片的焊接作为一个关键的工艺步骤,对焊接的严密性有着高度要求。如果电池漏液,就会形成废品。杂质或飞溅物都可能会导致焊缝出现微小的裂缝。因此,精准电焊密封销对于确保电池保持密封和电解液不外漏起着极其重要的作用。我们的目标是以较低和局部范围内的热量输入实现无变形和严密的焊缝。每个焊缝都可以进行在线检测、评估和记录。我们的系统可以检测出不规则和由缺陷的焊缝。100%确保流程的可追溯性和透明度。
查看更多信息
针对不同应用的不同电池类型
电动汽车通常使用三种类型的锂离子电池。这些电池依据相同的功能原理运作,具有较高的能量密度,可确保较长的续航里程。我们使用袋式电池、圆柱形电池和棱柱形电池,然后将它们连接成电池模块,以提供所需的电力。但这些电池类型有何区别?