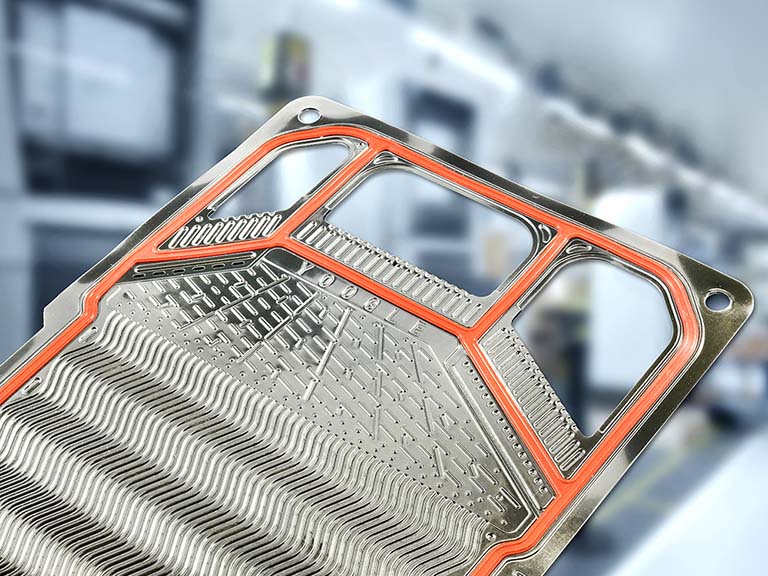
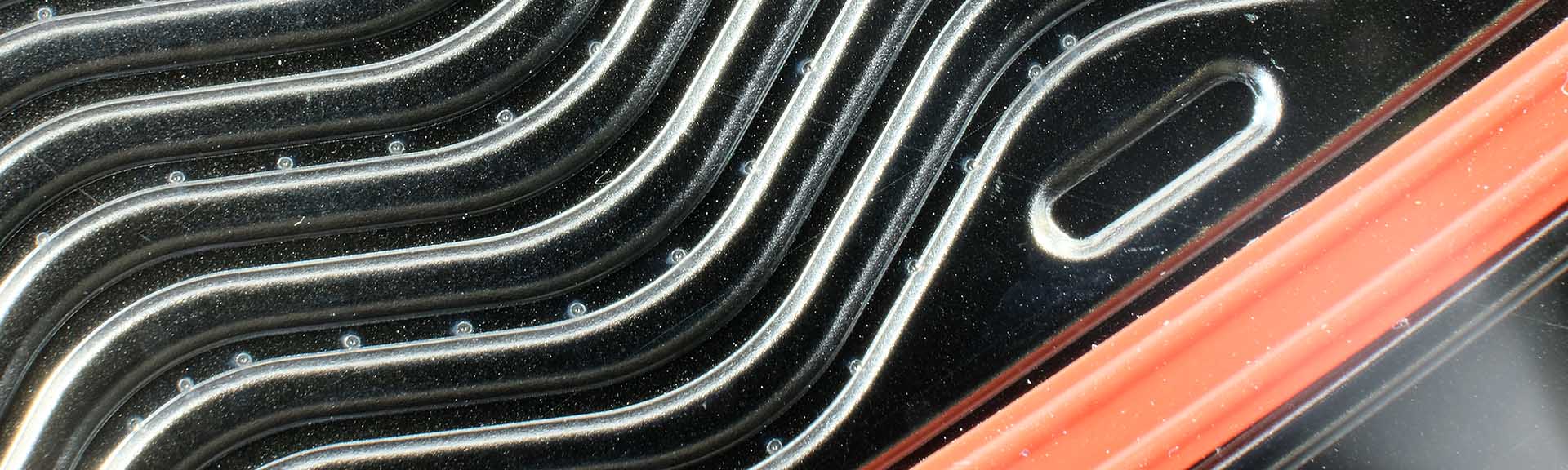
创新的 3D 测量技术和激光切割光学技术实现燃料电池的精确生产
电动汽车的能源要么来自电池,要么来自燃料电池。燃料电池由堆栈组成,即层层叠加。单个元件包括双极板、垫片、气体扩散层 (GDL) 和膜电极组件 (MEA)。
无论使用的是金属双极板还是石墨双极板,对我们的 3D 测量技术的要求都是相似的。这涉及到几何参数的精确测量,如通道深度和通道间距、通道网的位置、通道的粗糙度或塑料层或金属层厚度的测定。特别是在确定层厚度时,我们可以依靠不同的技术来分析透明层和非透明层。
金属双极板是厚度约为 50 - 75 μm 的极片,通常采用冲压工艺。不过,金属板上的小孔是用激光切割的,这里使用的是我们的激光切割光学仪器。此外,单个双极板还可以焊接在一起。因此,根据双极板的大小和数量,一个燃料电池可包含约 500 米的激光焊缝。因此,对焊缝及其质量进行监控是大规模生产燃料电池的关键步骤。
燃料电池生产步骤的解决方案
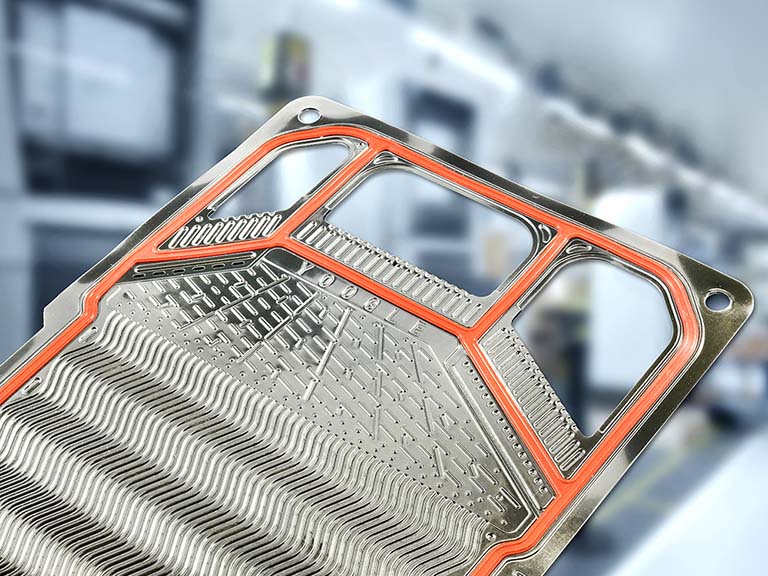
双极板是燃料电池的重要组成部分,它将电极和电解液分开,同时在电极之间传导电流。因此,两块厚度在50到100微米之间的板必须以气密的方式焊接在一起,形成稳定的导电结构。它们通常是由金属制成的,比如不锈钢。
在连接薄板的接触面时,焊缝通常非常窄且深,从而导致焊缝的强度和导电性很高。激光焊接可以有多种形式,如点(断续式或者连续式)或线(密封缝)。
每块双极板大约需要1米的焊缝。一个堆栈由大约400个双极板组成,因此需要400米的焊缝,且都必须符合最高质量标准。焊接必须紧密。为了实现高循环次数,焊接也必须进行得非常快,大约是600 - 800mm /s,即刚好低于所谓的驼峰限制。在焊接过程中,需要对生产过程进行仔细的监测和控制。我们的传感器可以检测到可能导致密封接缝泄漏的最小焊接缺陷。此外,监控系统还考虑到了密封焊缝的高速焊接或接触焊缝的短时间焊接。我们的采样率高达250kHz。
查看更多信息