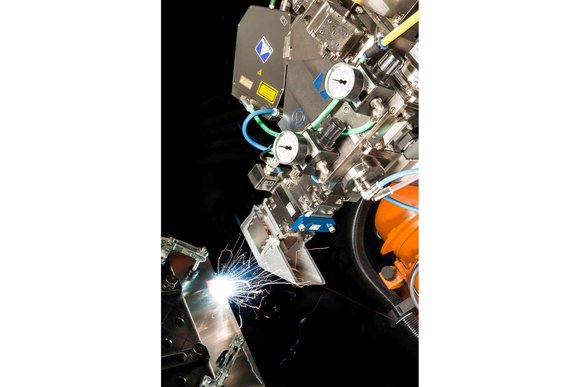
Precitec WeldMaster ScanTrack & Inspect – Process and quality control of laser beam remote welding for body-in-white work
Numerous trends characterise the use of lasers in the automotive area. The use of high-strength steels, weight-saving aluminium alloy, innovative joining technologies and unusual material mixtures leads to the superior target of making vehicles safer and more efficient. Nowadays, process monitoring systems around laser joining are very important in order to ensure both the process stability and the quality. Process monitoring is divided into pre-, in- and post-monitoring. The Precitec WeldMaster platform combines all different process steps. Both the online seam tracking and the seam monitoring can be realised during the laser welding process by means of laser triangulation and grey zone evaluation with only one camera.
The superior target of reducing the weight of vehicle bodies has a significant effect on the used materials and connection geometries. The introduction of aluminium in combination with short flanges reduces the weight on the one hand and leads to more complex joining processes on the other hand. Hot cracks are the biggest challenge in this context. The state-of-the-art is the use of silicon-based filler wires in order to reduce the number of resulting hot cracks.
WeldMaster
Due to the combination of the tracking functions of the Precitec WeldMaster with the ScanTracker scanning module and the laser power control, it is possible to address new process approaches. The ScanTracker is used in order to laterally oscillate the focussed laser beam and to superimpose it with high frequencies. Additionally, it is possible to apply a synchronous laser power modulation. This results in a precise power distribution in lateral direction, which makes the energy input to the workpiece locally soluble and thus significantly reduces the heat input and renders the filler material unnecessary.
Gap bridging
In case of fillet weld applications, it is possible to measure a possible gap between upper and lower sheet on the basis of laser triangulation prior to the actual laser process. The process parameters such as laser power, lateral position or power modulation of the laser beam can be adjusted accordingly. This leads to a controlled and robust gap bridging.
Quality monitoring
The seam geometry is an important indicator for the achieved quality. Defined geometric values, such as seam width, collapsed seams or seam bending can be measured directly in-situ subsequent to the processing and be evaluated by means of image processing. This is also based on laser triangulation and grey level analysis. As a consequence, the information on the quality of the component is available immediately, parts can be ejected and reworked instantaneously.
Customer benefits
Due to the use of the WeldMaster ScanTrack & Inspect for aluminium door production at the company Audi, it was possible to reduce the process time for the welding of relevant fillet welds by 53%. The increasingly important CO2 balance could be optimised by 24% due to the low energy input (-47%) and the associated declining laser power. Current costs, e.g. for filler wire or protection slide modules, could be reduced significantly by 95% [source: Audi AG, Dr. Jan-Philipp Weberpals, EALA2015, EALA2016].
Due to the possibility of in-situ quality monitoring, it is possible to completely dispense with separate subsequent stations in the production run. Consequently, the total investment could also be reduced by 24% due to the omission of separate quality monitoring stations and the necessary intermediate buffer [source: Audi AG, Dr. Jan-Philipp Weberpals, EALA2015, EALA2016].
By now, the WeldMaster ScanTrack & Inspect is used in series for applications around cars throughout the world. In addition to versatile aluminium applications, the WeldMaster can also be used for steel connections and compositions.
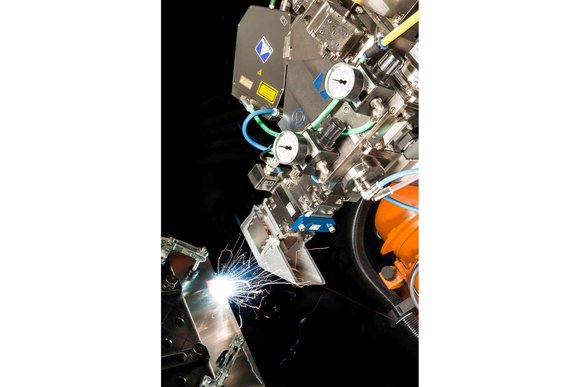